Applications of vibratory finishing
Vibratory finishing is everywhere—you just might not notice it. It smooths the edges of the screws holding your desk together, so they don’t catch your sleeve. It polishes the metal bits on your bike, making them shine even after rain.
Jewelry designers swear by it. A rough silver pendant goes in, and an hour later, it sparkles enough to catch light from across the room. Even tiny earrings get the treatment—no more prickly backs.
Big industries love it too. Car factories use it to finish hundreds of bolts in one go. Each bolt comes out with the same smooth feel, so mechanics don’t fumble with rough threads.
It’s not just metal. Granite countertops? Vibratory finishing takes them from dull to glossy, making spills easy to wipe. River rocks for your garden? A tumble in the machine turns them into polished gems that glow when wet.
Craft enthusiasts use it for handmade projects. Welded metal art, custom keychains, even vintage tool restorations—all get that professional look without hours of hand sanding.
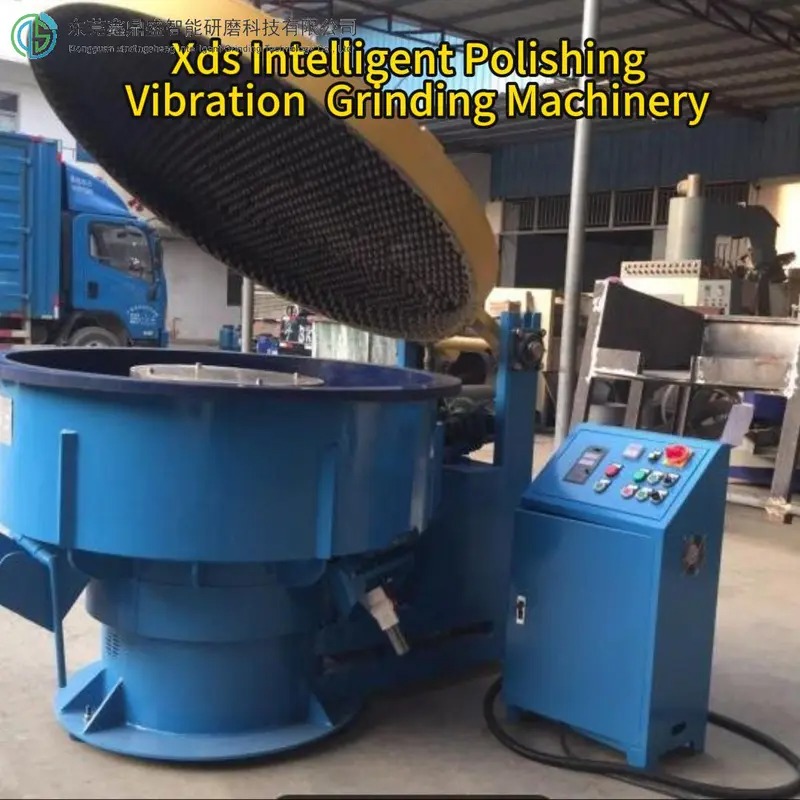
The process
Vibratory finishing is like giving parts a gentle scrub, but on steroids. Here’s how it works, step by step.
First, you load the machine. Toss in the parts that need work—say, a handful of rusty nails or a batch of rough stone beads. Then add the “scrubbers”: small, tough pieces called media. Think of media as tiny, reusable sandpaper.
Next, splash in a little water. It helps media stick to parts, so every nook gets polished. For extra shine, add a drop of special finishing fluid—kind of like soap for sparkle.
Close the lid and turn it on. The machine starts shaking—hard. Not just up and down, but side to side, in circles, all at once. This wild movement makes parts and media bounce off each other.
Each bump, rub, and slide shaves off a tiny bit of roughness. Burrs get knocked off. Rust flakes away. Surfaces get smoother, then shinier, the longer it runs.
When it’s done, you open the lid. Pour everything into a sieve to separate parts from media. Rinse the parts with clean water, dry them, and—boom—they look brand new.
No fancy skills needed. Even a beginner can do it. Just set it and forget it.
Media as a crucial agent for material finishing
Media is the unsung hero here. Without it, the machine would just shake parts around—no smoothing, no polishing.
It comes in all shapes. Small balls work for round parts like marbles. Cylinders get into tight spots, like the holes in a chain link. Odd, star-like shapes tackle tricky angles on jewelry or mechanical parts.
Materials matter too. Ceramic media is tough—it grinds down hard metals like steel or iron. Plastic media is softer, perfect for aluminum or copper, which scratch easily.
Some media is rough, with sharp edges for stripping rust or burrs. Others are smooth, made for polishing—they buff surfaces to a shine without leaving scratches.
You can even get colored media. It doesn’t change the finish, but it helps you tell different grits apart. No more mixing up rough and smooth media by accident.
Choosing the right media is key. Match it to your parts: soft media for soft materials, rough media for tough jobs. Get this right, and results look professional every time.
The Vibration & Finishing
The Oscillating Movement
Vibration is what makes the magic happen. The machine doesn’t just shake—it moves in a special way called oscillating.
Oscillating means it sways back and forth, up and down, all at once. It’s like jiggling a bucket of marbles while spinning it—every marble bumps into the others.
This movement forces parts and media to rub against each other constantly. Every bump shaves off a tiny bit of rough surface. Over time, those tiny bits add up to a smooth finish.
The speed matters. Most machines vibrate at high frequencies—fast enough to make the media dance, but not so fast that parts get damaged. It’s a sweet spot that balances speed and safety.
You can’t see it, but this motion is super consistent. Every part gets the same amount of rubbing, so they all look identical. No more one shiny bolt and one dull one in the same batch.
Types of vibratory finishing equipment
Not all vibratory finishing machines are the same. Each type handles different jobs.
Three-dimensional vibratory grinders
These are the workhorses for small parts. They’re usually round or square, with a deep basin. Perfect for screws, nuts, jewelry, or small stones.
They take up little space—some fit on a tabletop. But don’t let size fool you. A 700L model can handle hundreds of parts at once.
Horizontal vibratory grinders
These are longer and flatter, like a shallow tub. They’re made for big or long parts: golf clubs, metal shafts, or large stone slabs.
Parts lie flat in them, so they don’t get tangled. The horizontal shake ensures even contact with media, even for odd shapes like curved tool handles.
Automated models
Some machines come with extras. Automatic loading pours parts in for you. Automatic sorting separates finished parts from media. Great for factories, but home users can skip them.
Most have soundproof covers. They muffle the noise, so you can run the machine in a garage or basement without disturbing anyone.
Types of vibratory finishing equipment
Vibratory finishing equipment comes in a range of styles, each built to tackle specific jobs. The right one depends on what you’re polishing—size, shape, and how many parts you need to finish at once. Let’s break down the main types, so you can pick the best fit.
Three-dimensional vibratory machines
These are the workhorses of small to medium jobs. Shaped like deep bowls or square tubs, they use a high-frequency shake that moves in all directions—up, down, and side to side. This 3D motion ensures every nook of your parts gets polished, from the surface of a coin to the grooves of a screw.
They’re compact enough for home workshops or garage benches, with capacities ranging from 50L (small enough for jewelry) to 700L (big enough for batches of hardware). Many have built-in drains to make cleaning up water and grit easy. If you’re working with tiny parts—earrings, watch gears, or beads—this is your go-to.
Horizontal vibratory machines
Long and low, these look like rectangular tubs. They’re designed for parts that are too big or long for bowl-shaped machines: think golf club shafts, metal pipes, or large stone slabs. Instead of shaking in all directions, they vibrate horizontally, which lets long parts lie flat without bending or getting tangled.
Their extended length (some over 2 meters) means you can finish a dozen golf clubs at once, or a set of curtain rods, without crowding. They often come with soundproof lids to muffle noise, making them usable in small shops. If your parts are longer than 30cm, or have odd shapes like curved tool handles, horizontal is the way to go.
Tumbler-style machines
These are the portable, no-fuss option. Smaller than a microwave, they look like sealed canisters that shake back and forth. They’re perfect for hobbyists or crafters who need to polish tiny parts on the go—think beads, fishing lures, or small metal charms.
They don’t hold much (usually 5–20L), but they’re affordable and super easy to use. Just load, plug in, and let them run. No fancy settings, no extra parts—great for beginners.
Automated systems
For factories or shops handling huge batches, automated vibratory machines are a game-changer. They add features like conveyor belts to load parts, sensors to check finish quality, and automatic sorting to separate media from parts. Some even refill water or media on their own, so you can run them all day without lifting a finger.
They’re bigger and pricier, but they save hours of labor. If you’re finishing hundreds of parts daily—like bolts for a car plant—automated is worth the investment.
No matter which type you choose, all vibratory machines share the same core goal: making rough parts smooth, without the hassle of hand sanding.
Model | Volume (L) | Weight (kg) | Power (kW) | Machine Size (mm) | Best For |
ZC-700A | 700 | 1400 | 15 | 1650 x 1350 x 1400 | Medium parts, batches |
ZC-1000A | 1000 | 1500 | 15 | 2035 x 1350 x 1400 | Large parts, golf clubs |
ZC-2000A | 2000 | 2050 | 20 | 2320 x 1610 x 1700 | Industrial batches, stones |
Choosing vibratory finishing equipment
Picking the right vibratory finishing machine is easier than you think. Start with your parts.
If you work with small stuff—earrings, screws, beads—a three-dimensional grinder is best. It’s compact and handles batches well.
For long or big parts—golf clubs, metal pipes, large stones—go horizontal. They have the space to lay parts flat, so they finish evenly.
Check the volume. A 700L machine holds more than enough for home projects. Factories might need 2000L models to handle huge batches.
Noise matters. If you’re working at home, get a machine with a soundproof cover. It cuts down the racket, so you won’t annoy the neighbors.
Look for extras if you need them. Automatic loading saves time for big batches. A lid that opens easily makes loading and unloading less of a hassle.
Don’t overbuy. A small machine works fine for hobby projects. You can always upgrade if you start handling bigger jobs.
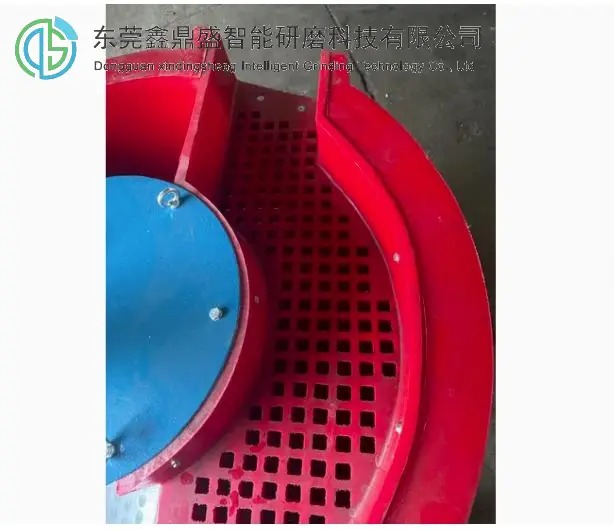
Running vibratory finishing equipment
Setting up
First, find a flat surface. The machine shakes a lot—if it’s wobbly, it might move across the floor. A sturdy table or workbench works best.
Plug it in. Most home models use regular outlets, but industrial ones might need more power. Check the label first.
Clean the basin. Old media or dirt can scratch new parts. Wipe it out with a damp cloth.
Loading
Add media first. Fill the basin about halfway. Too little, and parts won’t get enough rubbing. Too much, and they can’t move freely.
Drop in the parts. Spread them out—don’t pile them up. Crowded parts can scratch each other.
Add water. Just enough to make the media slightly damp. Too much, and parts float; too little, and media doesn’t stick
For polishing, squirt in a little finishing compound. It’s like liquid polish that helps media buff surfaces to a shine.
Starting and monitoring
Close the lid. Some machines have a latch to keep it from popping open during shaking.
Turn it on. You’ll hear a loud hum—that’s normal. Let it run
Check progress after 30 minutes. Use tongs to pull out a part. If it’s still rough, let it go longer. Soft metals might need an hour; hard ones could take 2–3.
Finishing up
Turn off the machine. Wait for it to stop completely—no reaching in while it’s shaking.
Open the lid. Use a sieve to scoop out parts and media. Shake the sieve to separate them.
Rinse parts with clean water. Scrub gently if there’s leftover grit. Dry them with a soft cloth or let them air dry.
Put media back in the machine for next time. It’s reusable—you can use it dozens of times before replacing.
Conclusion
Vibratory finishing is a game-changer for anyone who works with metal, stone, or hard materials. It’s easy, fast, and turns rough parts into polished gems.
You don’t need to be an expert. Load, turn on, wait, unload—that’s all it takes. It handles small hobby projects and big factory batches equally well.
Whether you’re fixing up old tools, making jewelry, or prepping parts for sale, it gets the job done. Give it a try, and you’ll wonder how you ever managed with sandpaper and elbow grease.
FAQ
Q: How long does it take to finish parts?
A: It depends. Small, slightly rough parts might need 30 minutes. Big, rusty ones could take 3–4 hours.
Q: Can it damage my parts?
A: Rarely. Use soft media for soft metals like aluminum. Don’t run it longer than needed—over-polishing can wear parts down.
Q: Do I need to replace media often?
A: No. It lasts for dozens of uses. Replace it when it looks worn—smaller than when you bought it, or covered in gunk.
Q: Can I mix different parts in one batch?
A: Only if they’re the same material. Mixing metal and stone, for example, might scratch the softer one.
Q: Is it expensive to run?
A: Not really. It uses little electricity. Media is reusable, and water costs next to nothing. Perfect for hobby budgets.